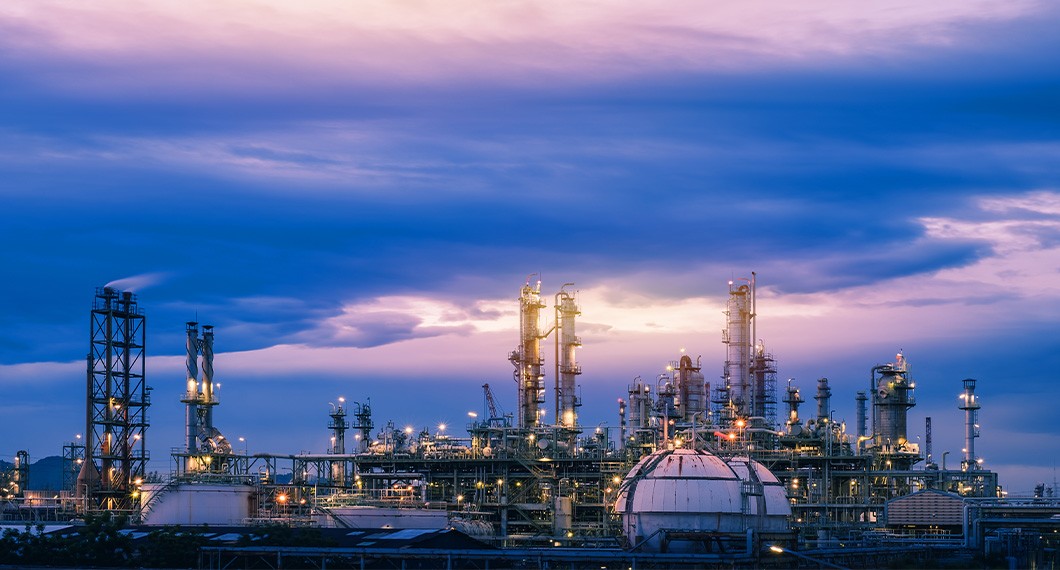
Understanding Hazardous Locations and the challenges of monitoring them
Electrical equipment can and does cause explosions in some atmospheres. As cameras and senor capabilities increase, these cameras are being used in more areas than ever. In the past, one of the limiting factors was placing a camera in a critical area defined as hazardous. Hazardous areas are environments in which the atmosphere contains, or may possibly contain, flammable or explosive gases and, in the right conditions, may cause a fire or explosion. The frequency of occurrence determines the level of hazard for a location. The longer the material is present, the greater the risk. These areas present many challenges in terms of where you can place, maintain, and use a sensor. Explosion-protected cameras address some of these concerns and regulations.
To help define hazardous areas, a rating system was devised for definition of what can be used in a Hazardous Area. In short, areas that produce a certain level of gas, vapor or liquid that are present in normal operation conditions. Class/Division/Zone is the classification system set up in the US. For this discussion we will use the Class I Division I hazardous areas.
Class I, Division 1: There are three different situations that could exist to classify an area as a Class I, Division 1 location:
1. Ignitable concentrations of flammable gases or vapors may exist under normal operating conditions.
2. Ignitable concentrations of such gases or vapors may exist frequently because of repair or maintenance operations or because of leakage.
3. Breakdown or faulty operation of equipment or processes might release ignitable concentrations of flammable gases or vapors and might also cause simultaneous failure of electric equipment.
The control and monitoring of equipment to ensure sustained processing activity is essential in refineries and industrial plants to control production and operational cost. Companies are always looking to increase production, drive down the cost of production and improve environmental performance in refineries. In the past, most of the monitoring relied on individual people walking an area to be the eyes and ears for any problems. Sensors were introduced and embedded in processing areas to monitor vibration, heat, and the like. Verification once a sensor alarmed was confirmed by still having to send in a person to validate the alarm. Cameras today can be the eyes and ears of a human to validate remotely without disruption to process operation or production thus reducing production costs.
As we investigate a typical oil and processing area, we see the hazardous area and the CID1 with ignitable concentrations present as defined. We also see many process monitoring applications present. Such applications include:
· Rotating equipment – equipment that could come out of balance triggering a vibration sensor
· A thermal couple area – areas that could heat up too fast or exceed processing limitations. Many products are developed by mixing and adding chemical at a precise temperature for the chemical reaction to occur properly. I.e. antifreeze
· Valves and seals – junction points controlling volume tend to leak and fail.
· Settling tanks – used for separations during process. Monitored by thermal couples
· Pumps and pumping stations – looking for seal failure and early leaks
· Piping – miles and miles of pipes can be monitored for leaks and wear or damage
Using sensors such as visible and thermal cameras can help in monitoring and verify problems in some of these applications, remotely without shutdown or the risk of sending a person in that area.
Challenges in remote monitoring in hazardous areas
Some challenges in remote monitoring in hazardous areas involve access to equipment for maintenance and reducing failure points. Shut down for maintenance is costly in lost production. Unscheduled shutdowns are very costly. Easy quick installations with reduced crews because of lighter camera systems and no additional equipment needed to boost or extend network signals help reduce production downtime. New cabling solutions like the GameChanger CableTM from Paige, deliver 1Gb/s Ethernet and PoE+ up to 656 feet or 10Mbs/s up to 850 feet reducing costs, simplifying installs and saving money. By extending the distance limitation with cable alone, installers are also avoiding the need to install (and later service) equipment in remote and hazardous areas, saving money and keeping workers safe.
Preventive maintenance
Remote monitoring of these applications listed could help establish trend analysis and facilitate predictive maintenance thus allowing intelligent scheduling for preventive maintenance. Explosion-protected cameras are IP cameras that can be configured remotely, health monitored remotely and rebooted remotely reducing the need for human interaction in the hazardous areas.
Processing applications
Process capabilities of these cameras have increased significantly in the past several years. The ability to take an unacceptable image and process to get an acceptable usable image has never been more available than today. These sensors are now a computer with a lens. Users are seeing more in challenging conditions using this technology to verify and confirm before costly intervention.
On the edge analytics
The ability to run multiple event-driven edge analytics reduces bandwidth use lowering costs and automates our monitoring process for implementation of AI (Artificial Intelligence) and ML (Machine Learning). Edge based analytics can not only tell you if a person is entering an area that is restricted (safety, security) but can also notify if it see a rise in temperature of a failing component or detect a leaking pipe or emissions.
New markets and applications
As we see the cost of explosion-protected cameras go down, we see other verticals opening such as agriculture (processing plants, storage facilities, transportation lines, fuel distribution terminals), chemical (fertilizer plants, chemical facilities) transportation and water treatment facilities all having hazardous areas associated. These verticals also have common applications within their own plants requiring explosion-protected cameras and sensors. Automating critical monitoring not only reduces overall production costs but positions companies for the new digital age to come.